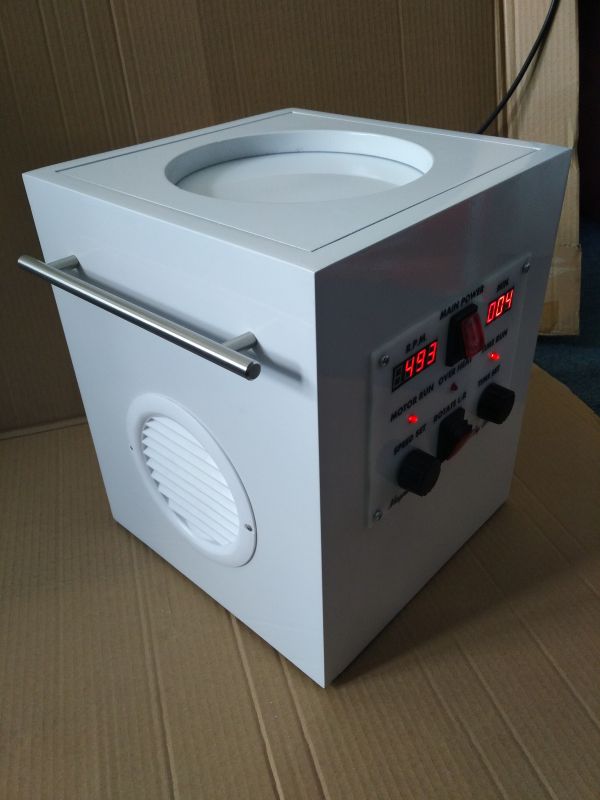
Vor ungefähr drei Monaten fragte mich mein Freund, ob ich einen Magnetpolierer für seinen Kollegen Juwelier bauen würde. Ich fragte, was ist es, was ist es? Hier entwickelte sich eine längere Diskussion, ein Austausch einiger E-Mails/SMS mit Links und ich wusste bereits mehr oder weniger, was die Maschine ist.
Das allgemeine Funktionsprinzip ist einfach. Wir haben eine sich drehende "Platte", auf der vier starke Neodym-Magnete montiert sind. Zwei von ihnen befinden sich nahe der Außenkante der Platte und sind mit dem N-Pol nach oben gerichtet, und die anderen beiden befinden sich nahe der Mitte der Platte und sind mit dem S-Pol nach oben gerichtet. Dadurch entsteht eine Art rotierende Magnetfeldwelle, die das Material abwechselnd anzieht und abstößt. Und das Material sind Nadeln... Aber mehr dazu später.
Ich werde hier nicht über alle aufgetretenen Schwierigkeiten und Probleme schreiben, da der Bau 3 Monate statt der geplanten 2-3 Wochen dauerte.
Ich werde das Gerät kurz beschreiben und Fotos zeigen. Vielleicht wird es in Zukunft für jemanden nützlich sein. Die Kosten für die Bauteile zuzüglich unerwarteter Kosten betragen ca. 400 EUR zuzüglich Arbeitskosten. Insgesamt etwa die Hälfte dessen, was Sie für einen ähnlichen in der Fabrik hergestellten Magnetpolierer bezahlen müssen.
Jetzt ist es Zeit für ein paar Fotos vom Bau, denn darum geht es beim Heimwerken.
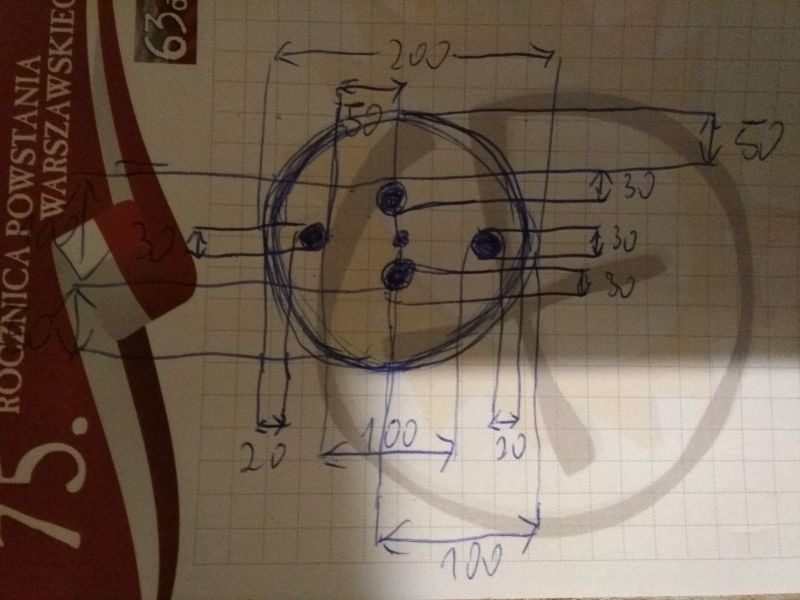
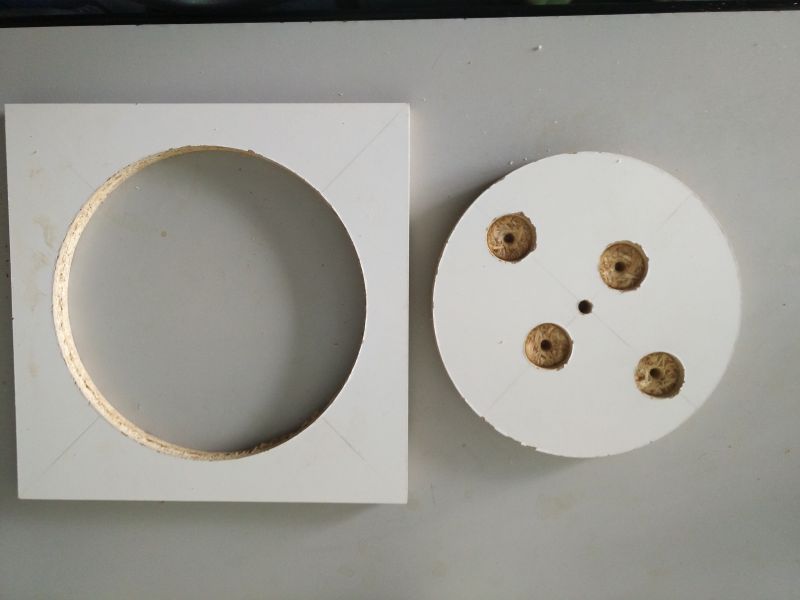
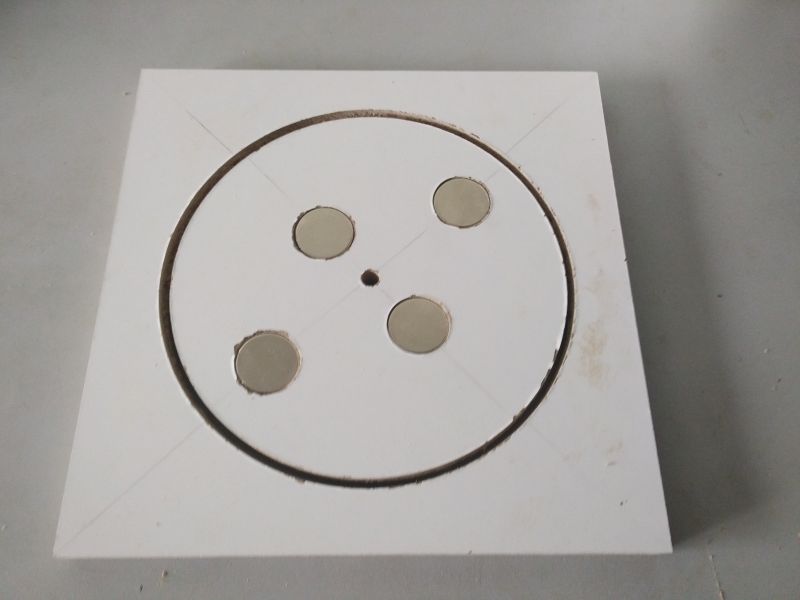
Es war der Teller.
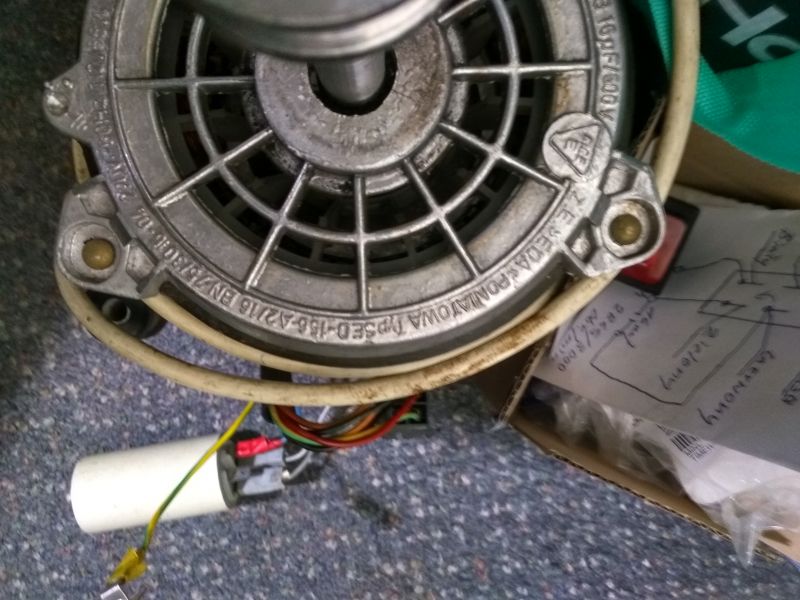
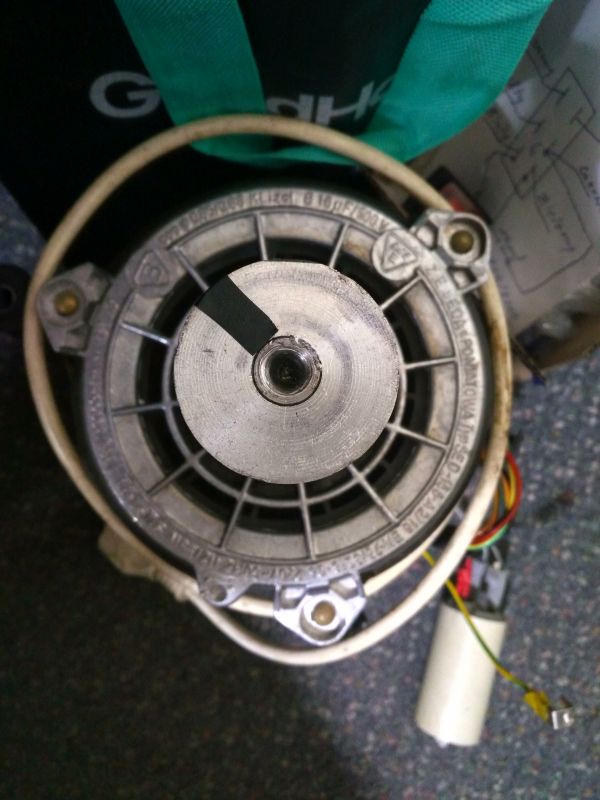
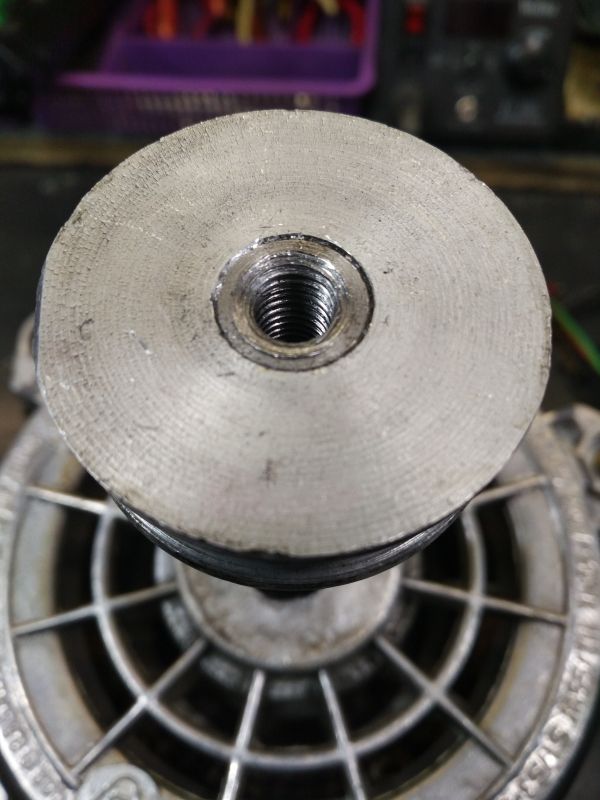
Hier ist der Motor, der sich als Mißerfolg herausstellte und für Drehstrom umgebaut werden musste. Dagegen bin ich stolz auf das Gewinde in der Welle. Da ich die Riemenscheibe in keiner Weise abziehen konnte, bohrte ich die Motorwelle ein und schnitt drin ein Gewinde. Keine Gewindebohrer für Blindgewinde verfügbar.
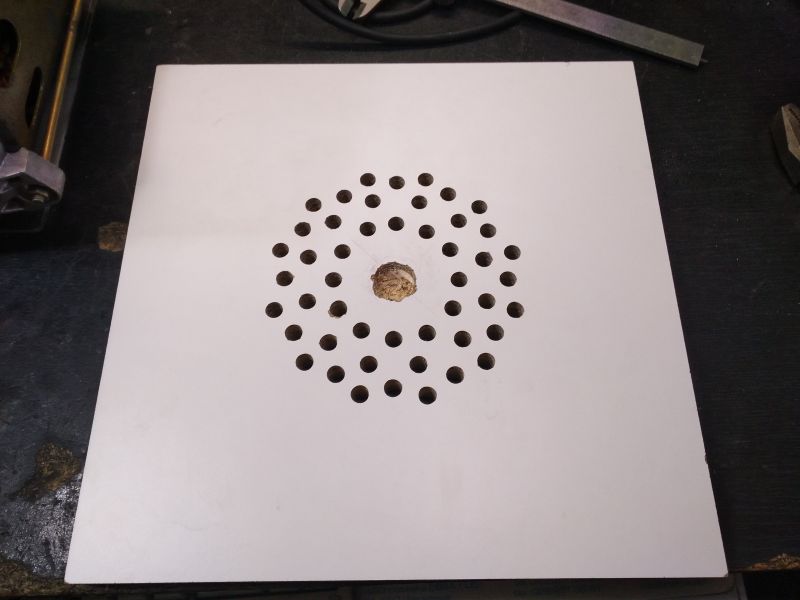
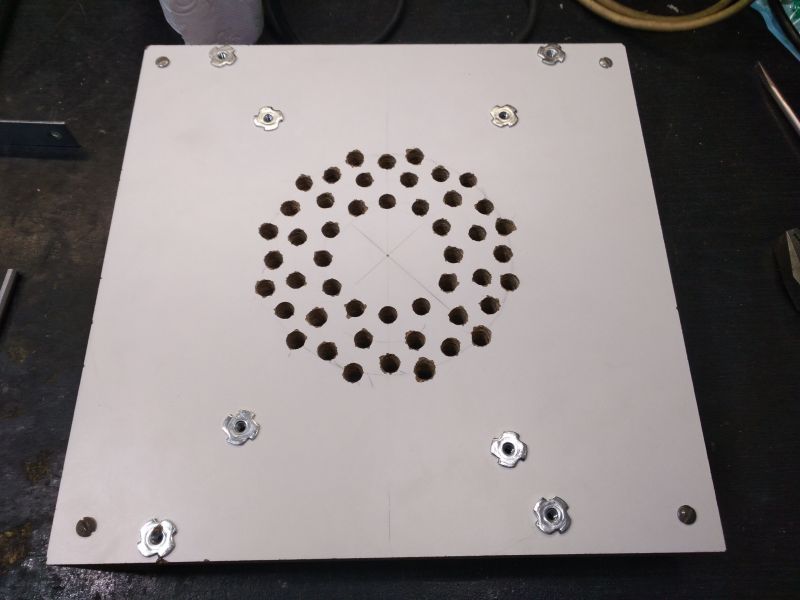
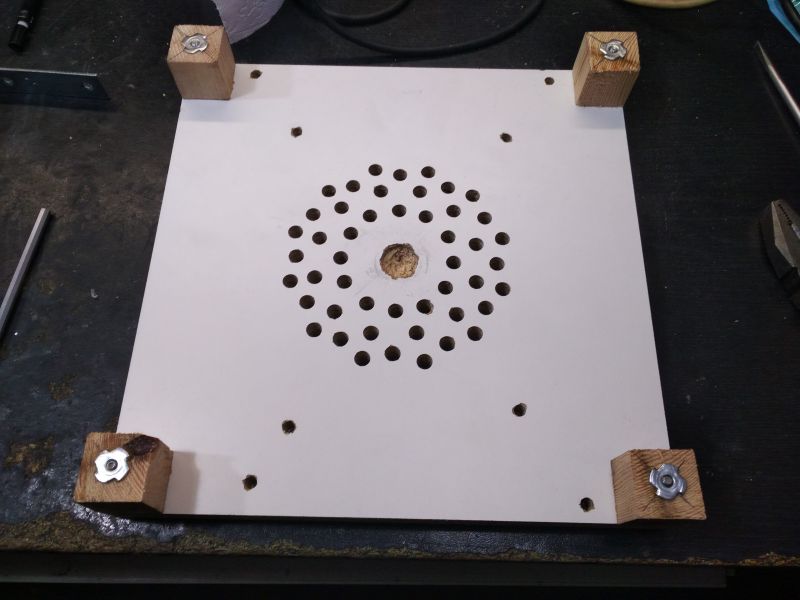
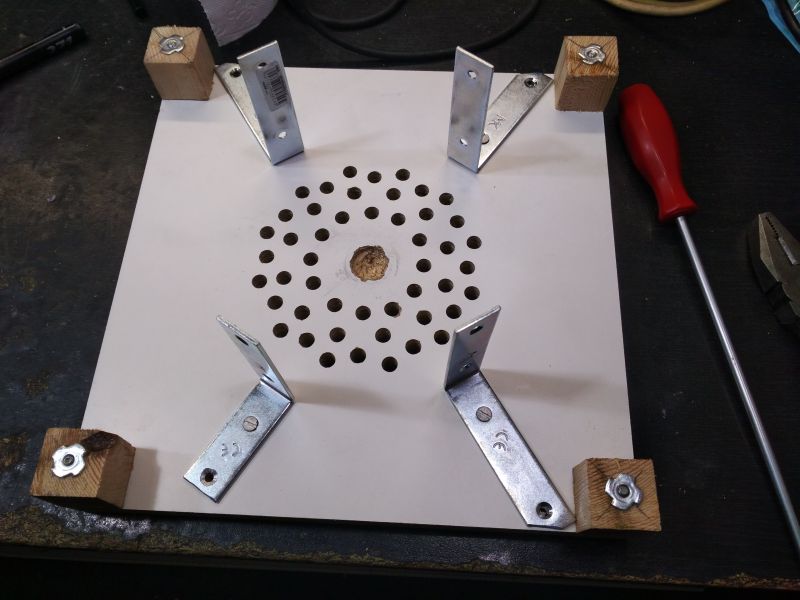
Gehäuseboden und Motorhalterung.
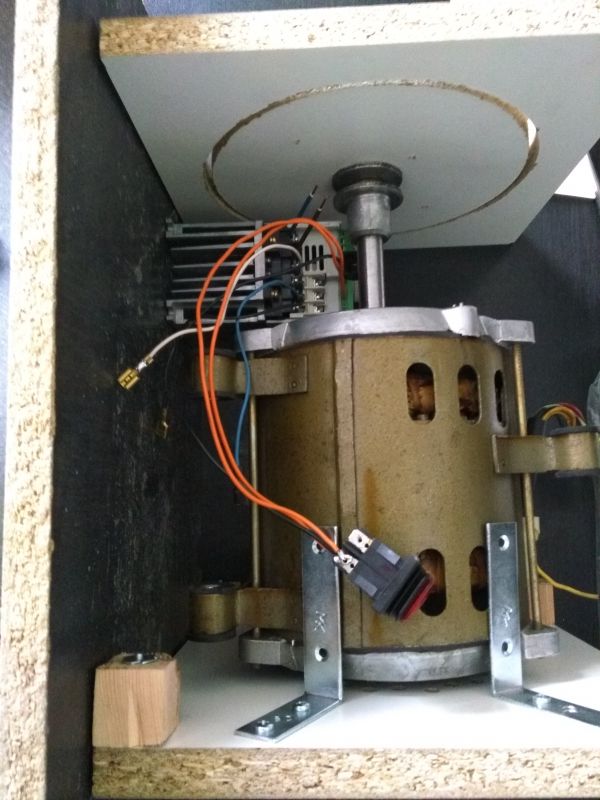
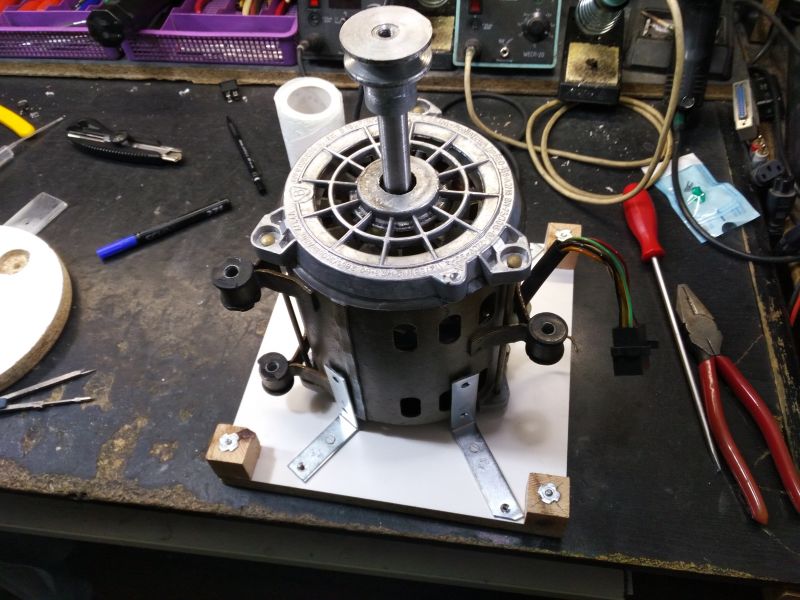
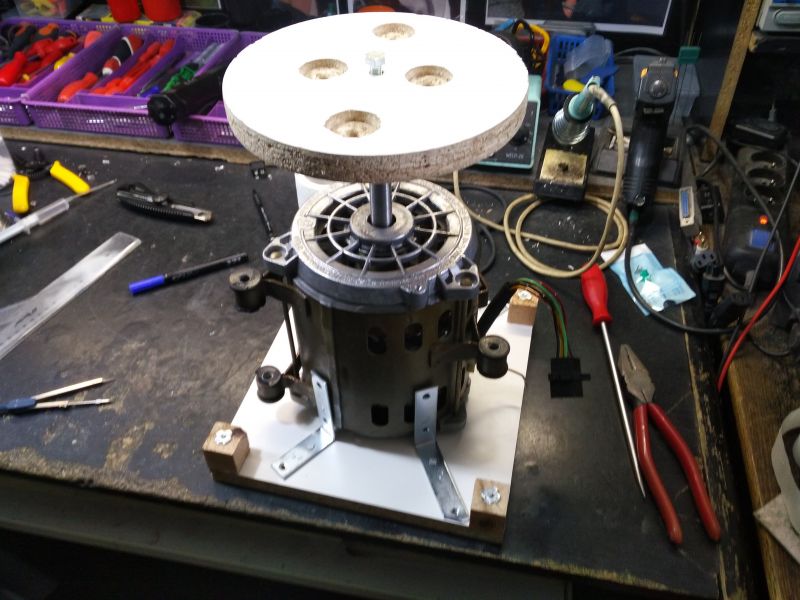
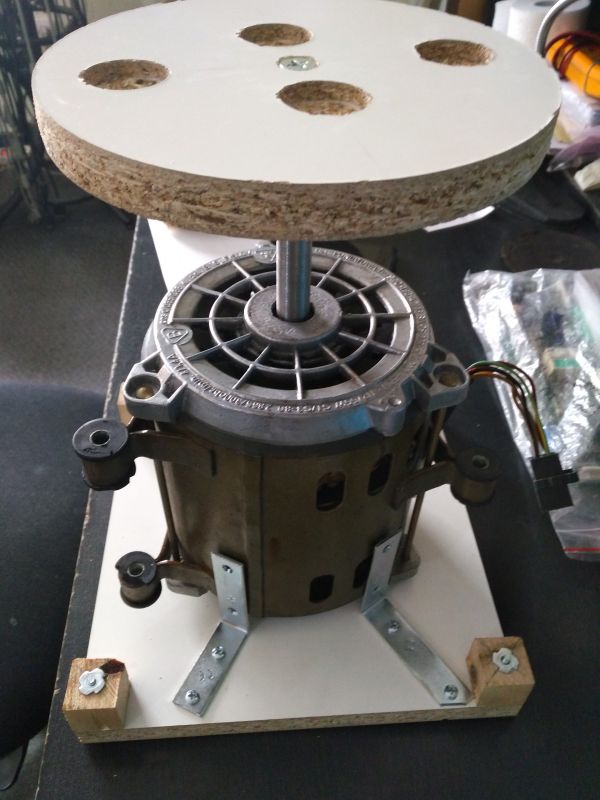
Und hier ist der Motor selbst mit einer Platte.
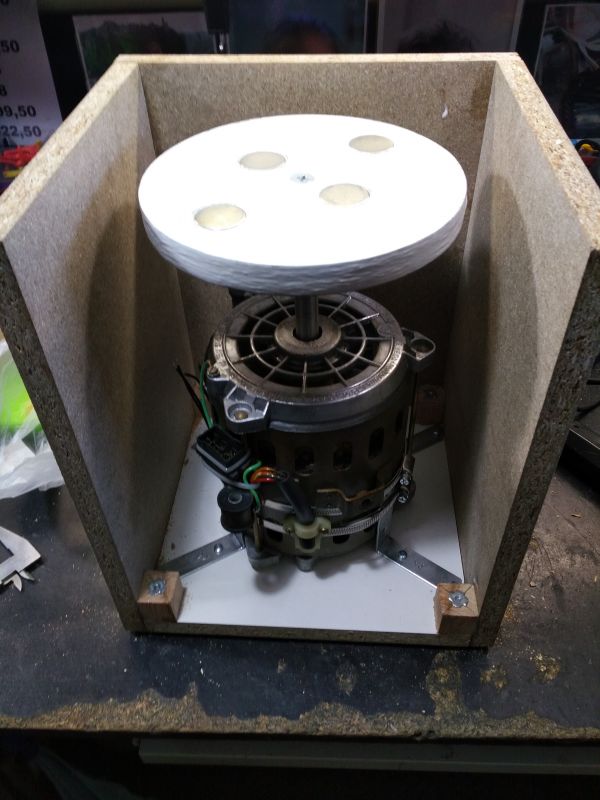
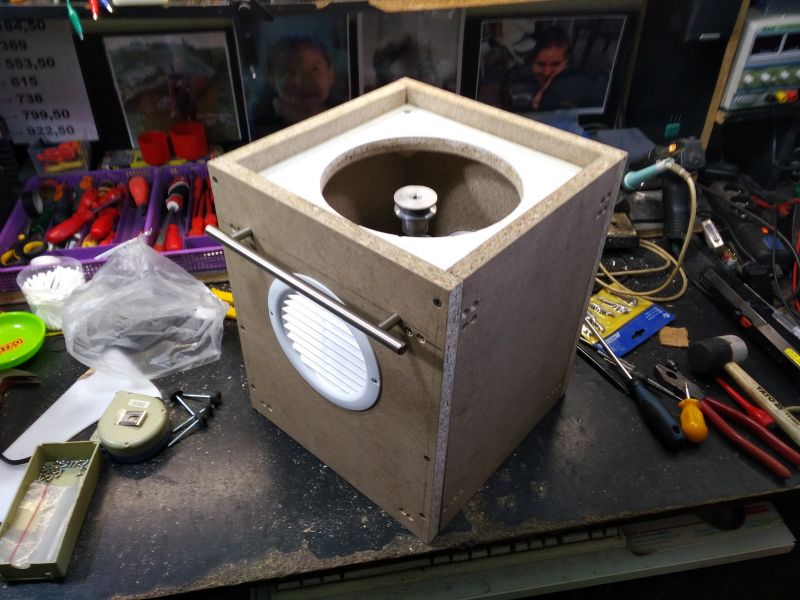
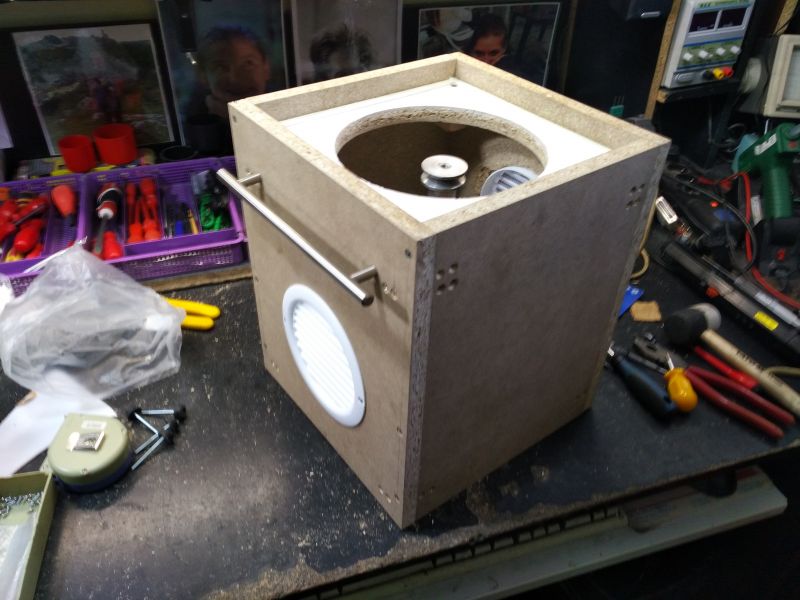
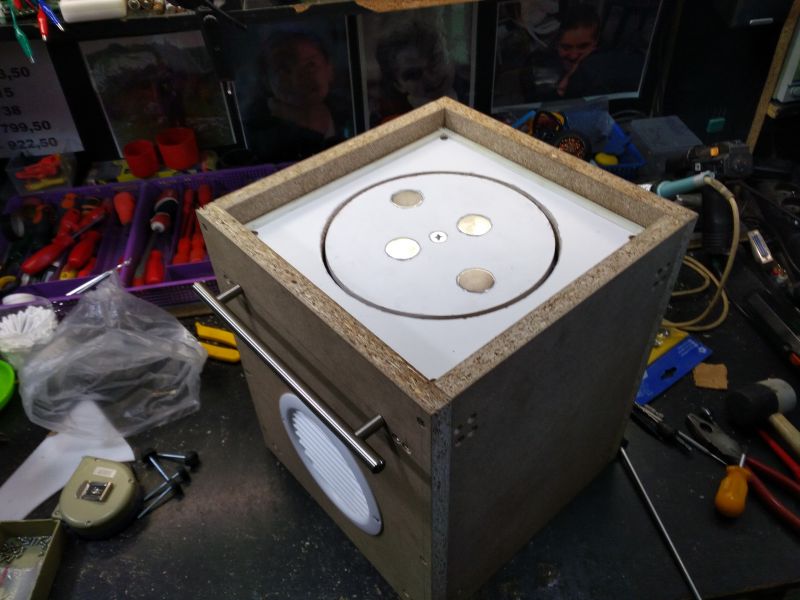
Die Arbeit schreitet voran, man sieht bereits einige Umrisse des Ganzen.
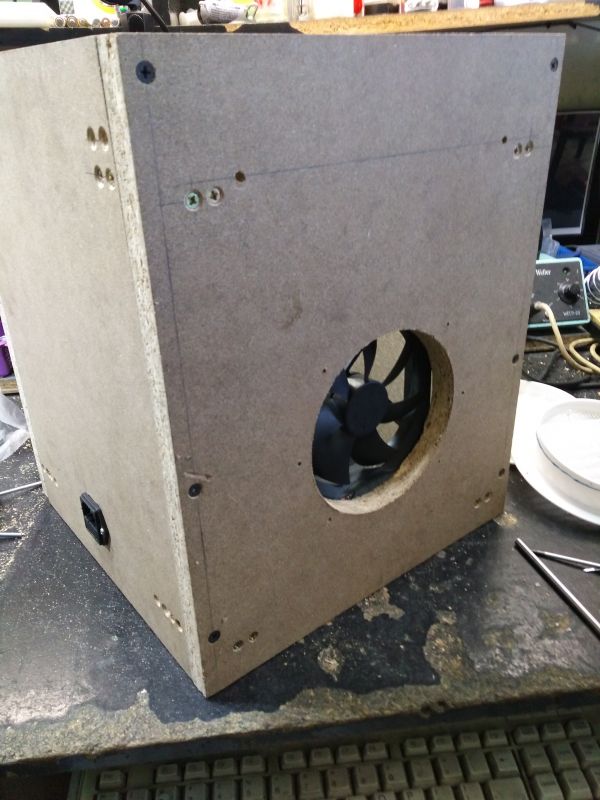
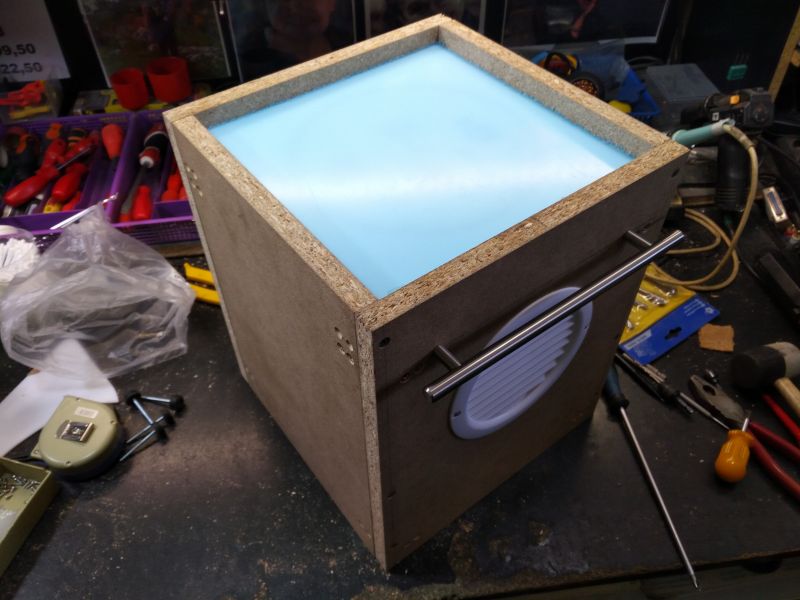
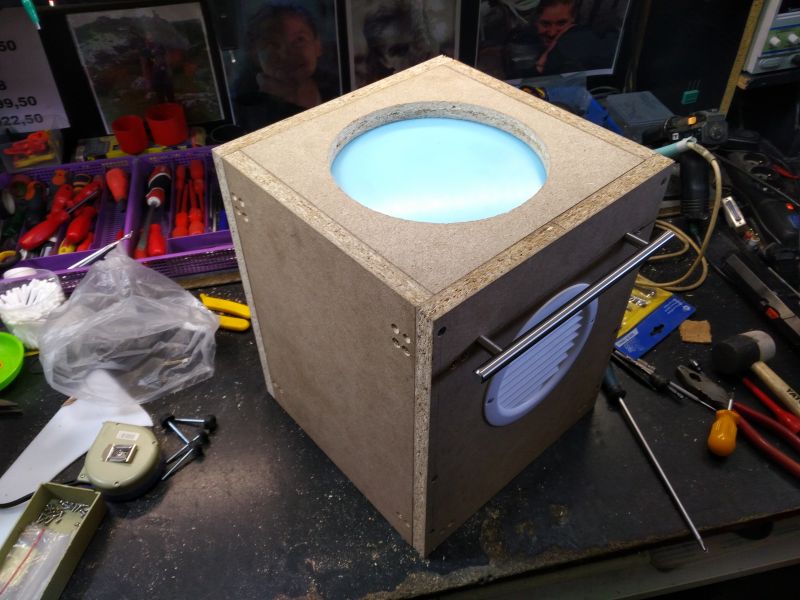
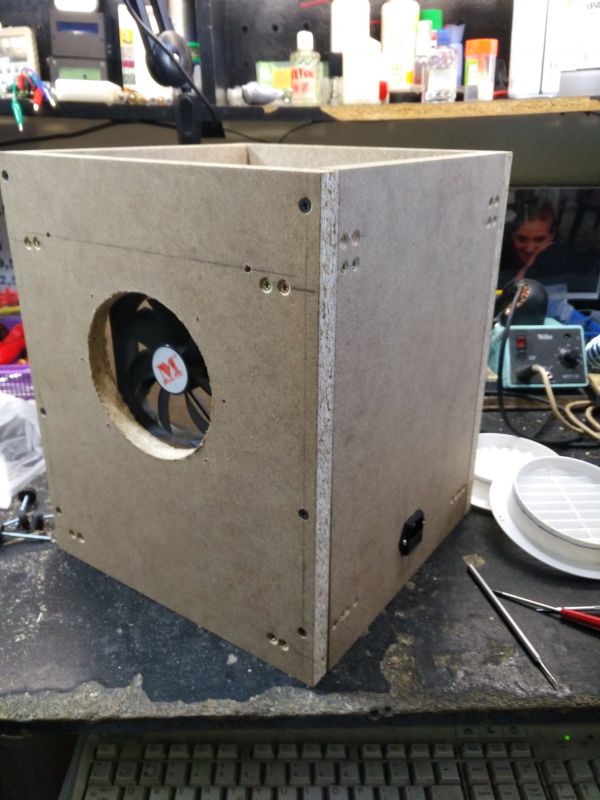
Das Finale rückt näher...
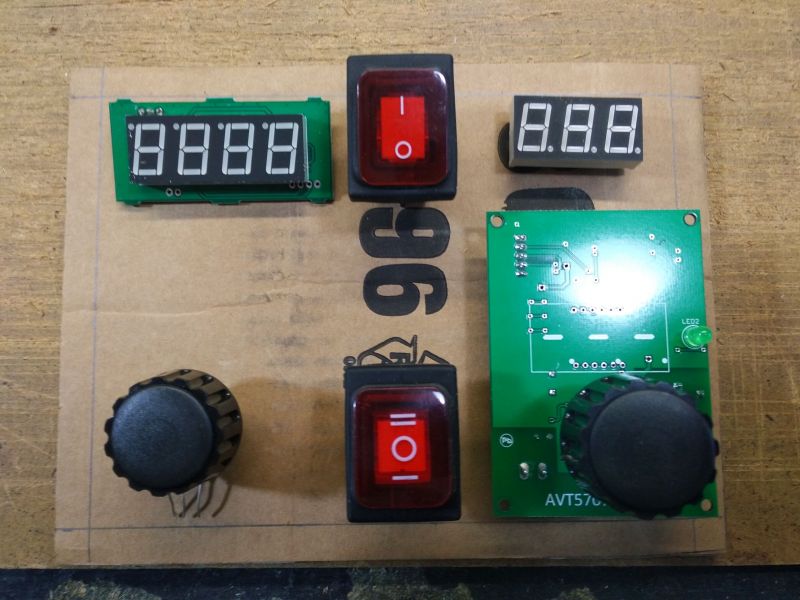
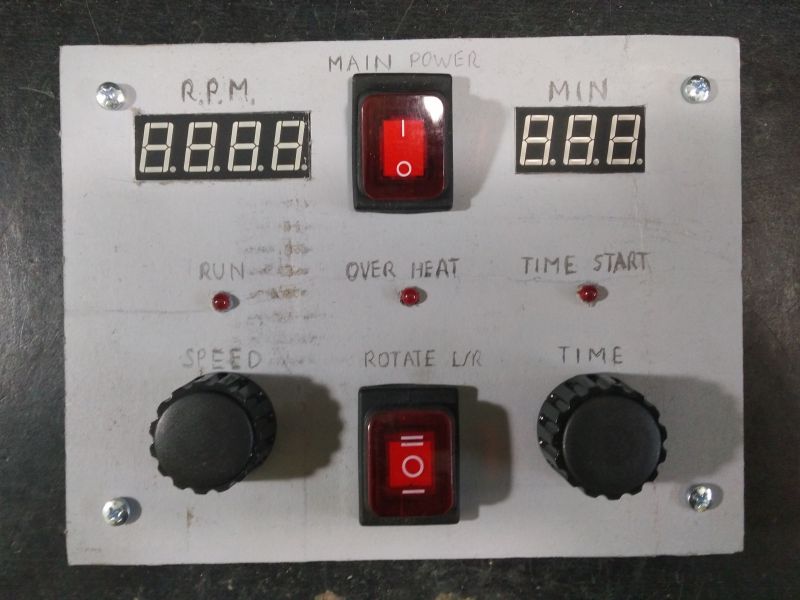
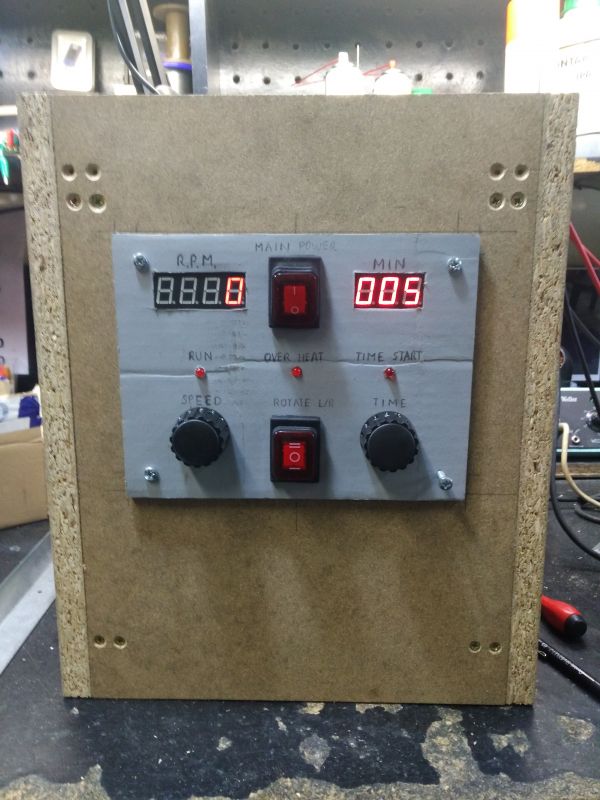
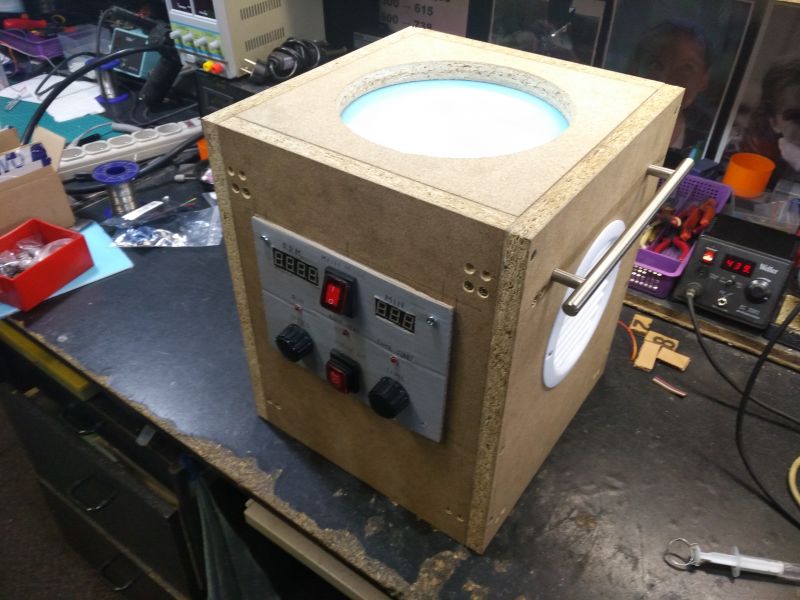
Vorentwurf der Frontplatte aus Wellpappe mit Skalpell geschnitten.
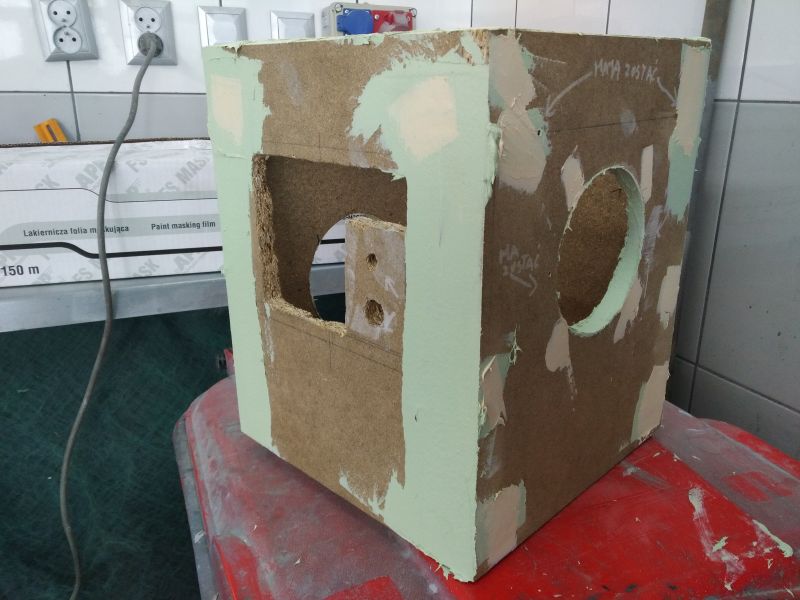
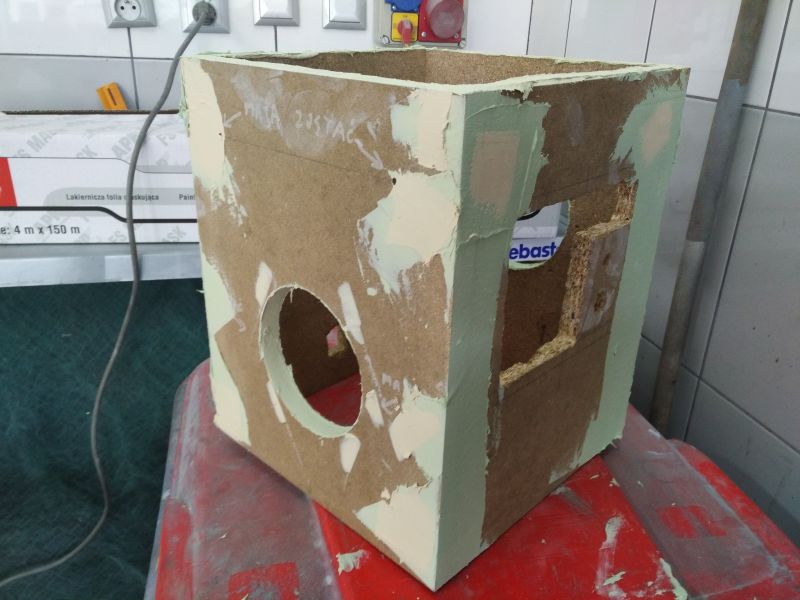
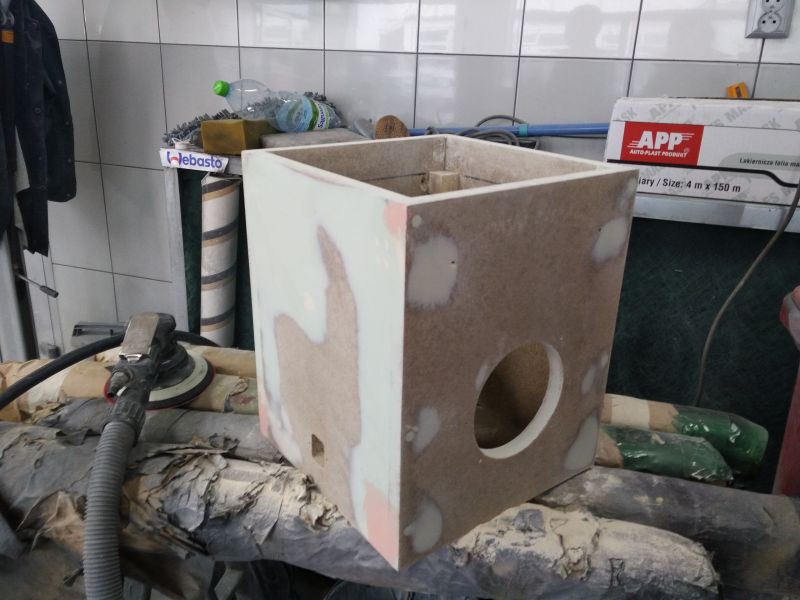
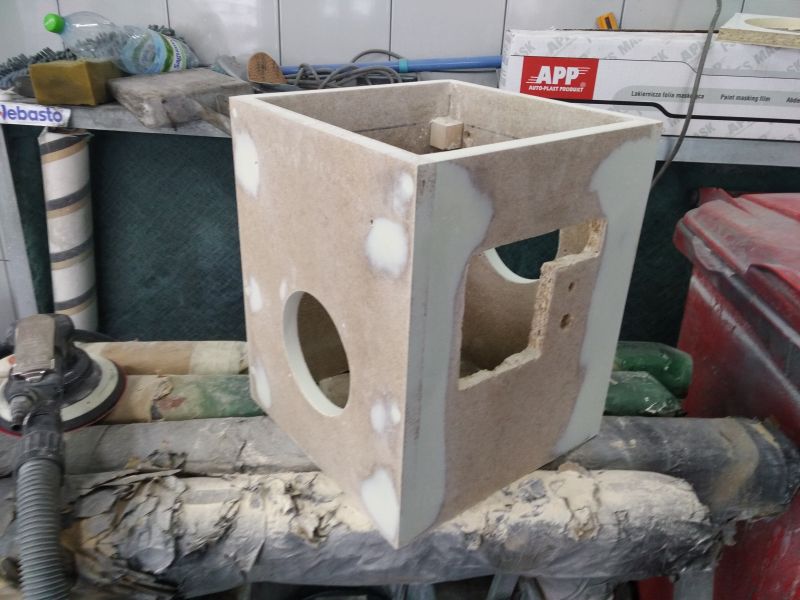
Und hier schpachteln...
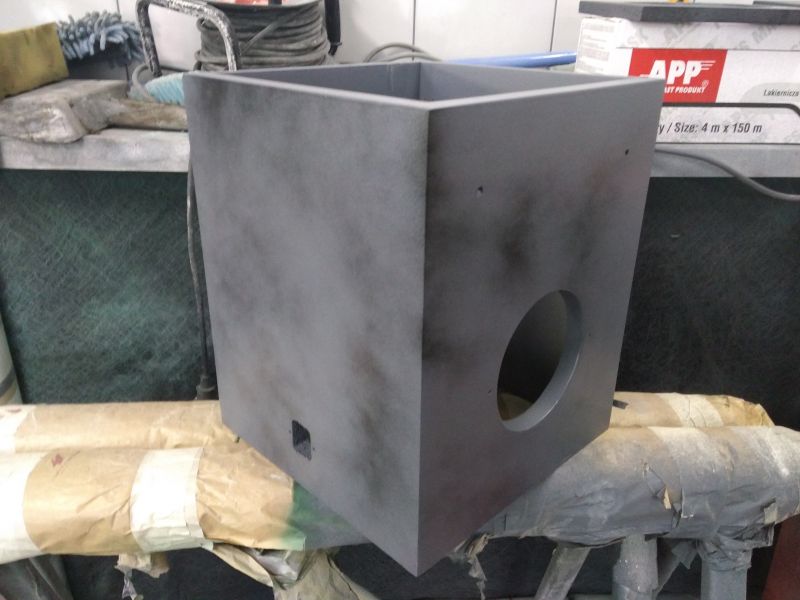
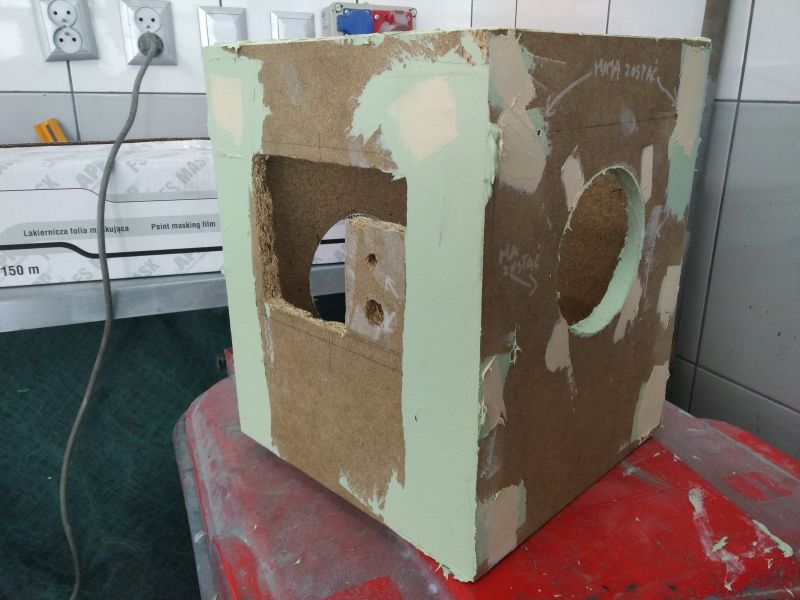
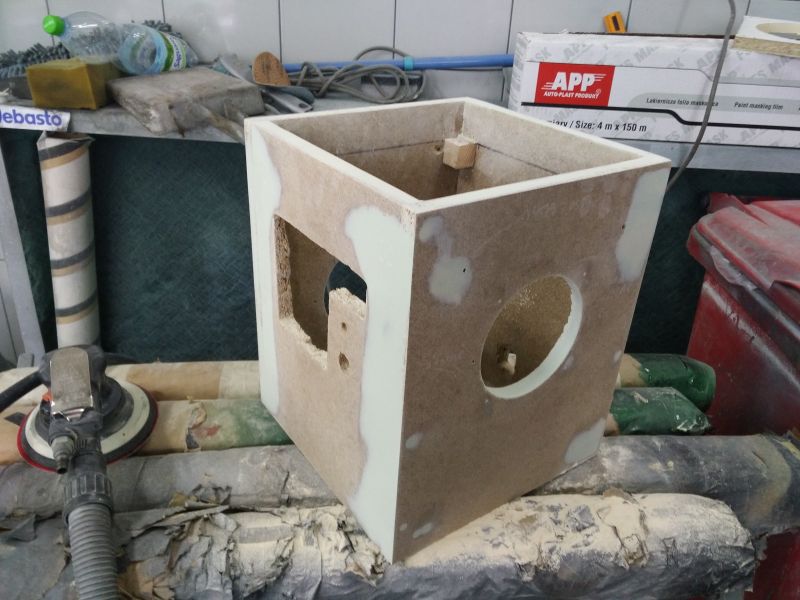
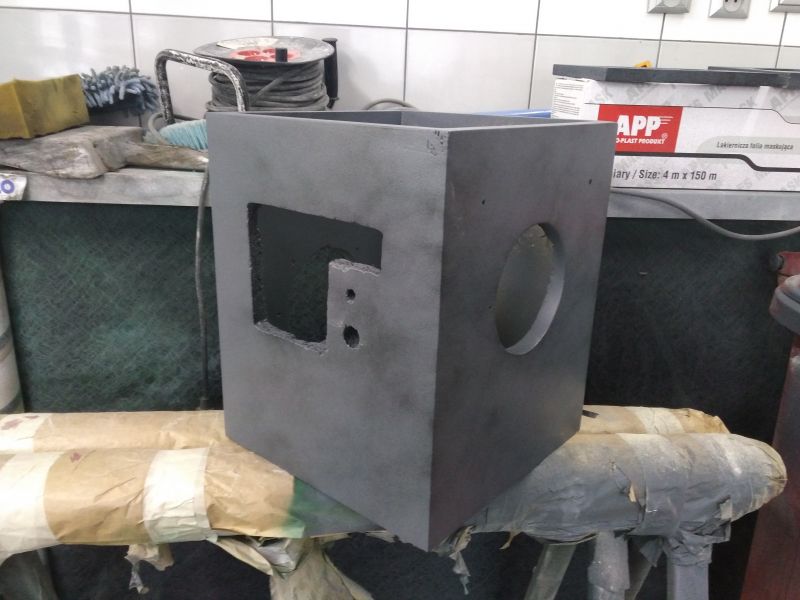
Mehr Spachtelmasse und Grundierung.
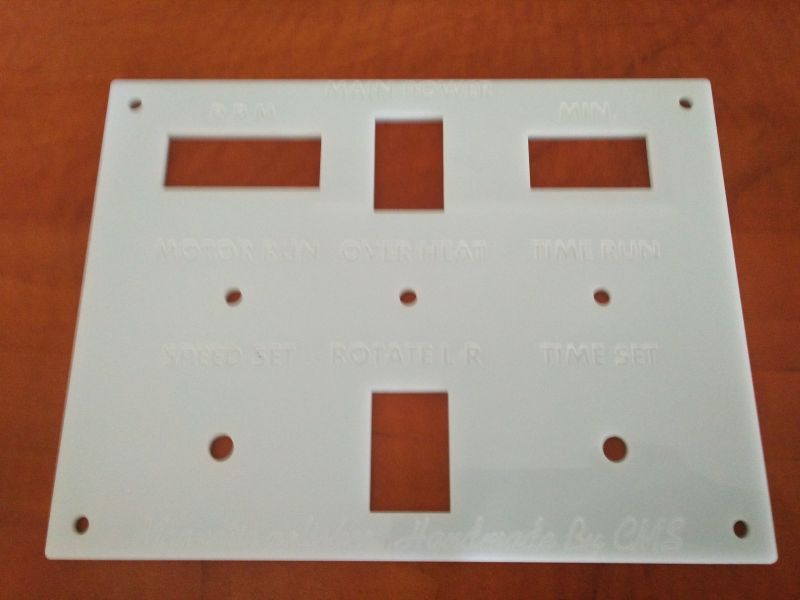
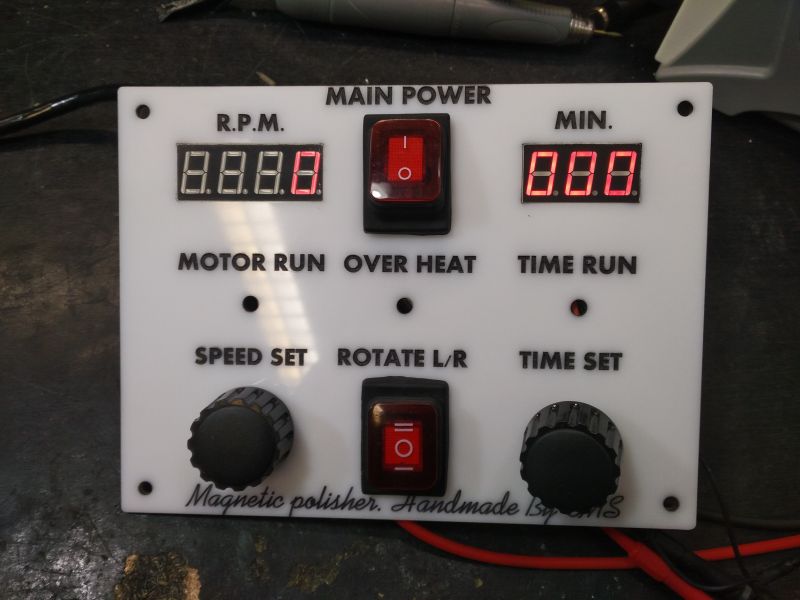
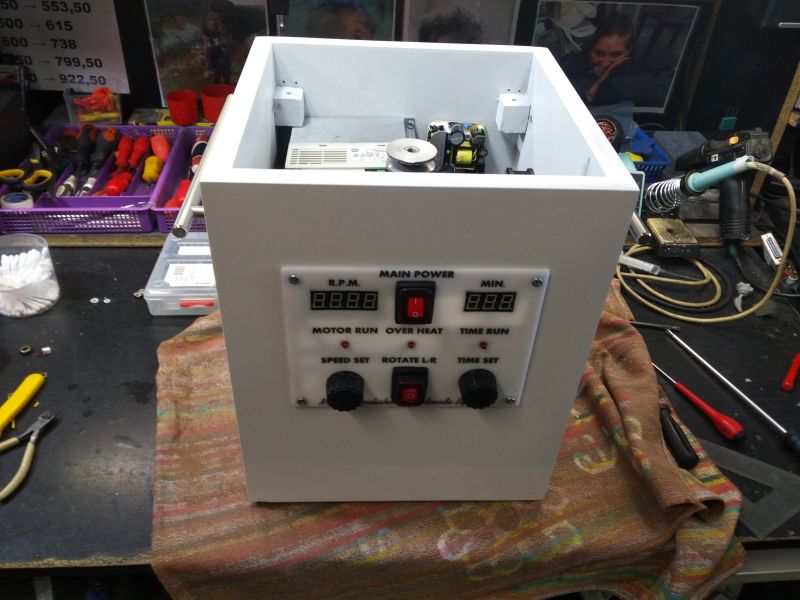
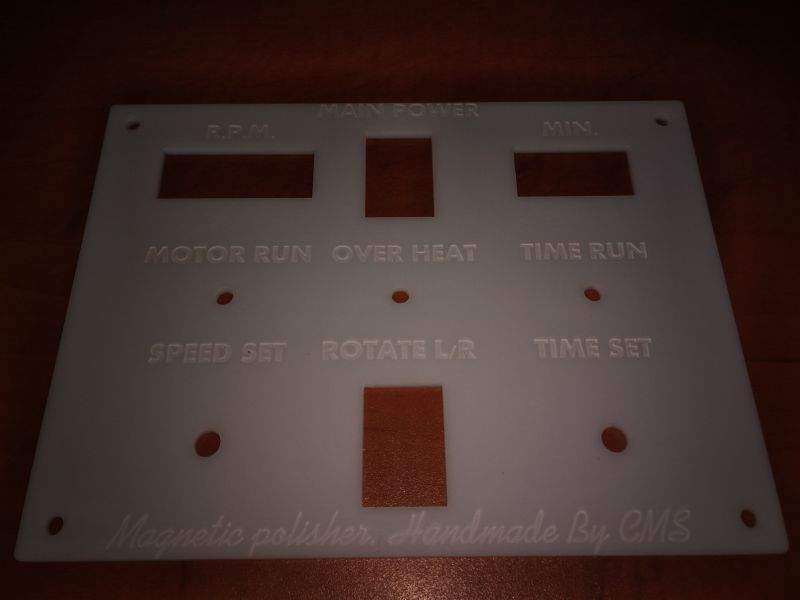
In der Zwischenzeit wurde eine Frontplatte aus Plexiglas erstellt, die Inschriften werden bis zu einer Tiefe von 0,5 mm auf einem Laserplotter eingraviert und mit Nitro-Lack gefüllt.
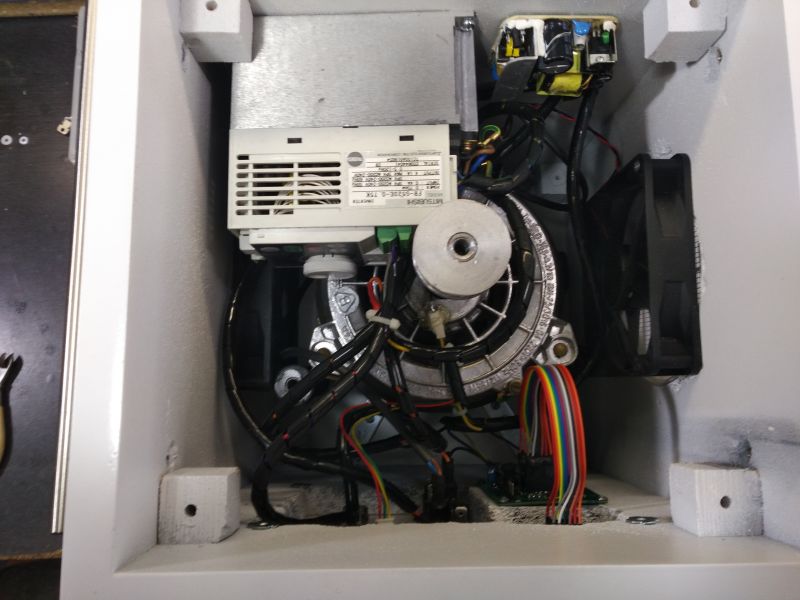
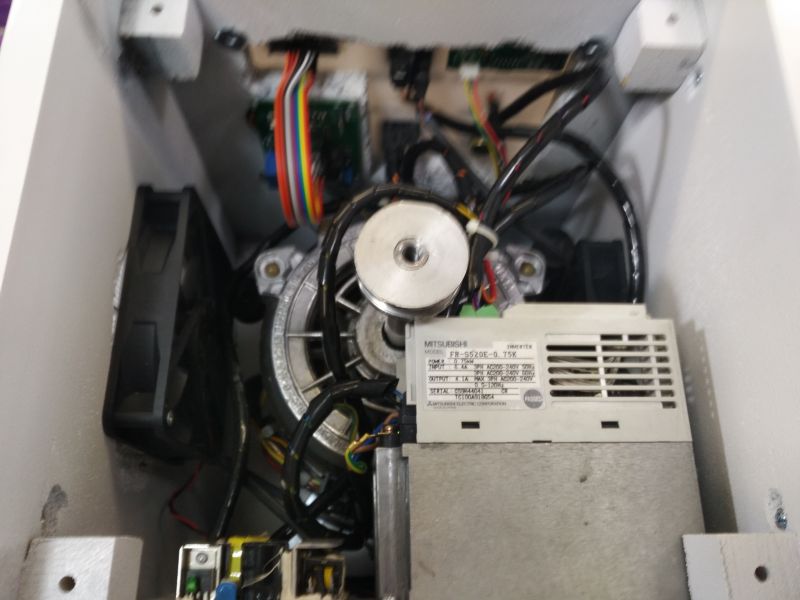
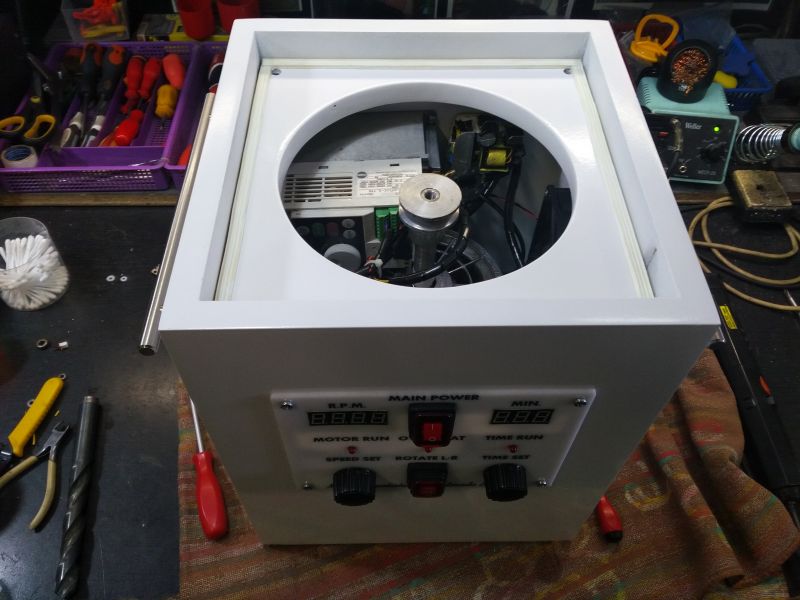
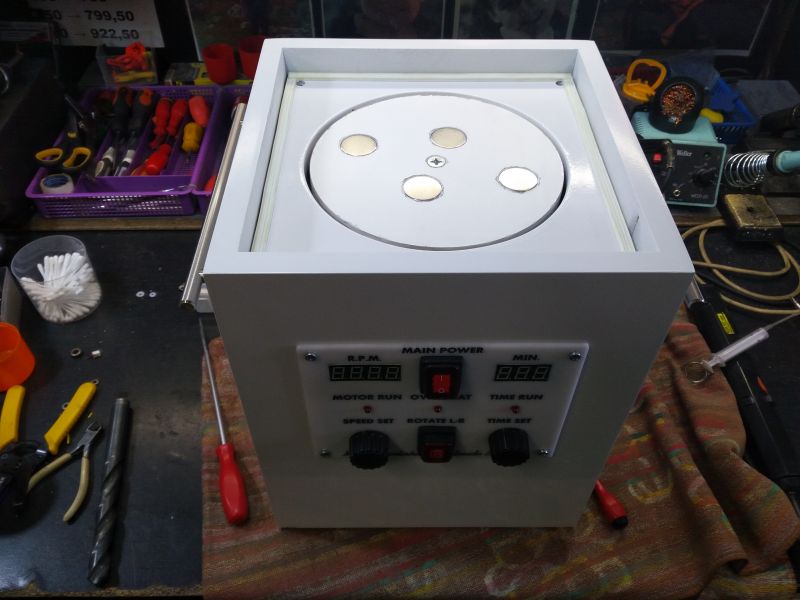
So sieht es innen aus.

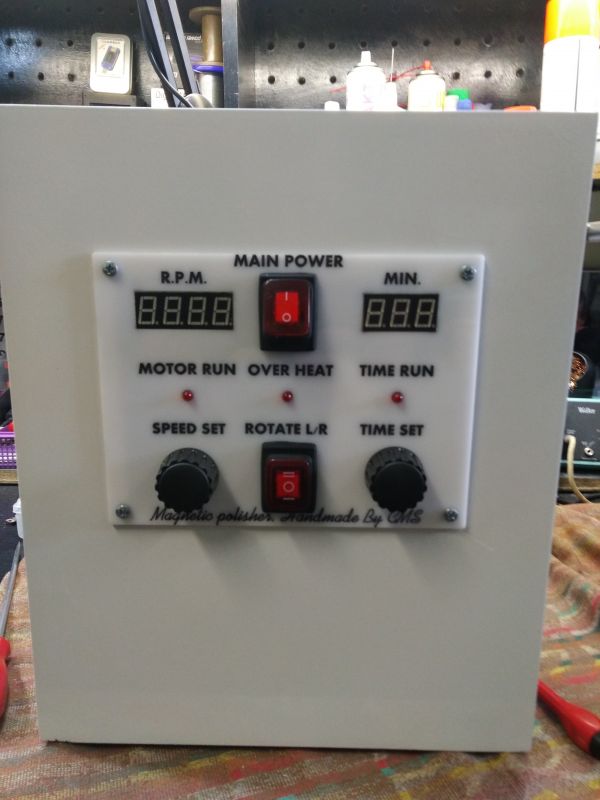
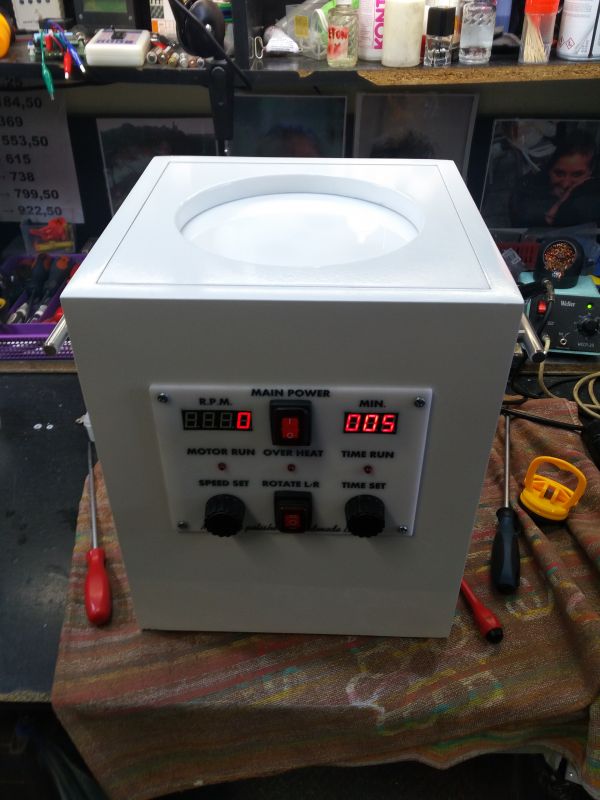
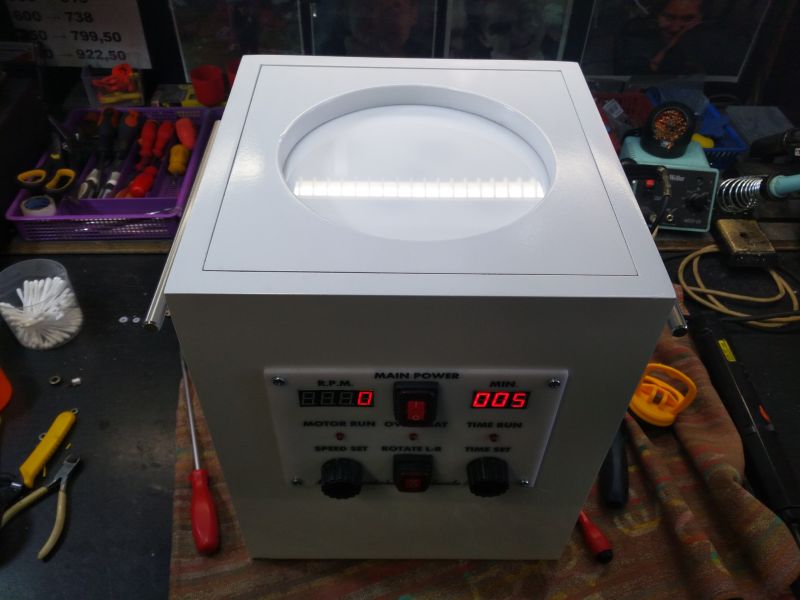
Und so von außen.
Ich werde hier keine Diagramme oder andere Dokumentationen veröffentlichen, da diese nicht erstellt wurden, und ich werde keine Dokumente absichtlich erstellen, da sich die Maschine bereits beim Kunden befindet.
Wenn jemand schlau ist und eine solche Maschine braucht, wird er sie bauen. Immerhin wusste ich vor drei Monaten nicht einmal, was es ist...
Ich möchte nur ein paar Fotos von der Konstruktion zeigen. Normalerweise präsentiere ich meine Designs nicht, auch nicht die mit hohem Standard, weil ich keine Zeit dafür habe. Aber dies ist das erste Mal, dass ich ein Gerät/eine Maschine dieses Typs sehe, und dies ist der einzige Grund, warum ich bereit bin, diese Konstruktion mit Ihnen zu teilen. Weil es interessant ist.
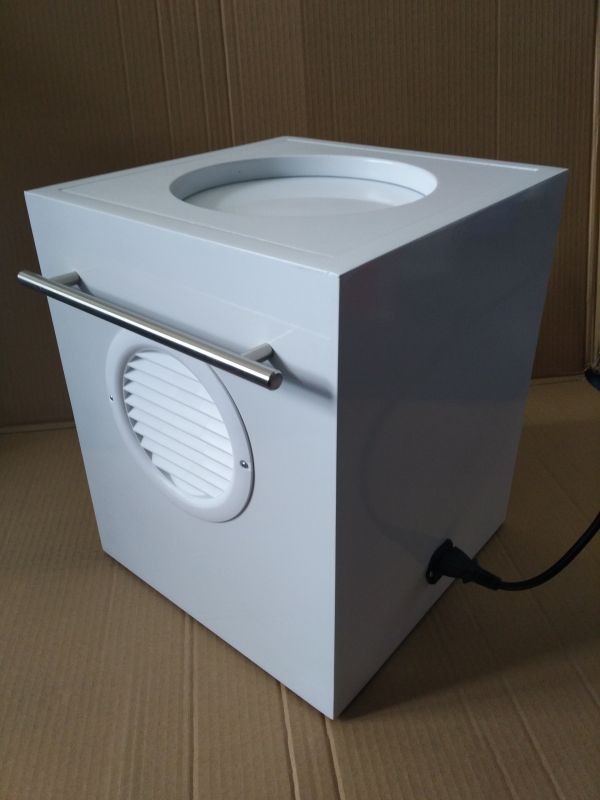
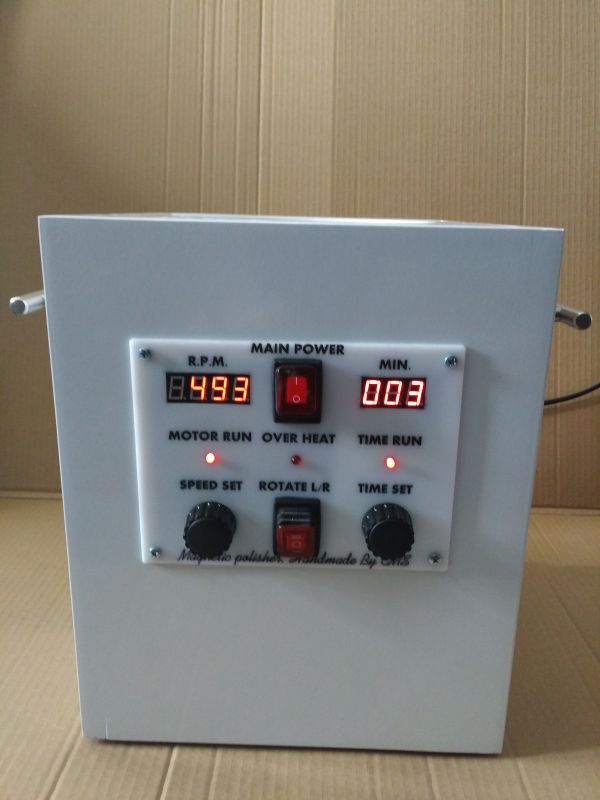
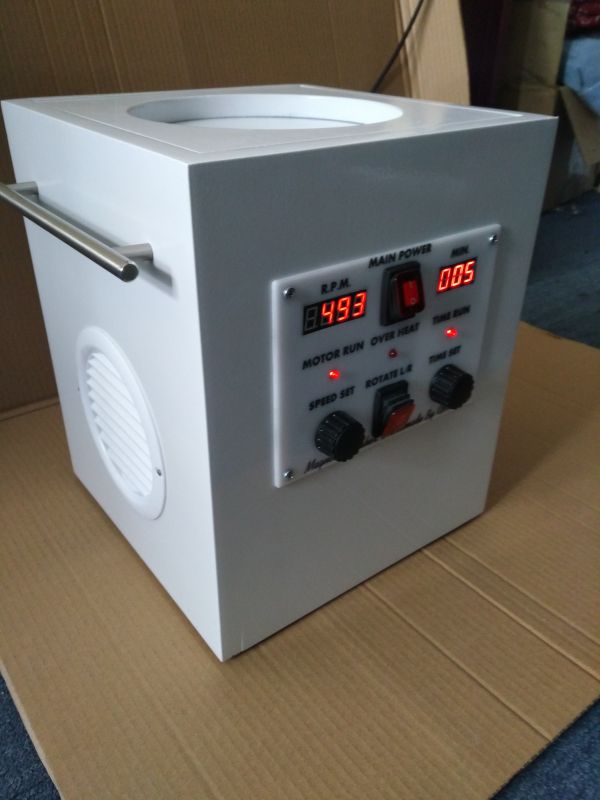
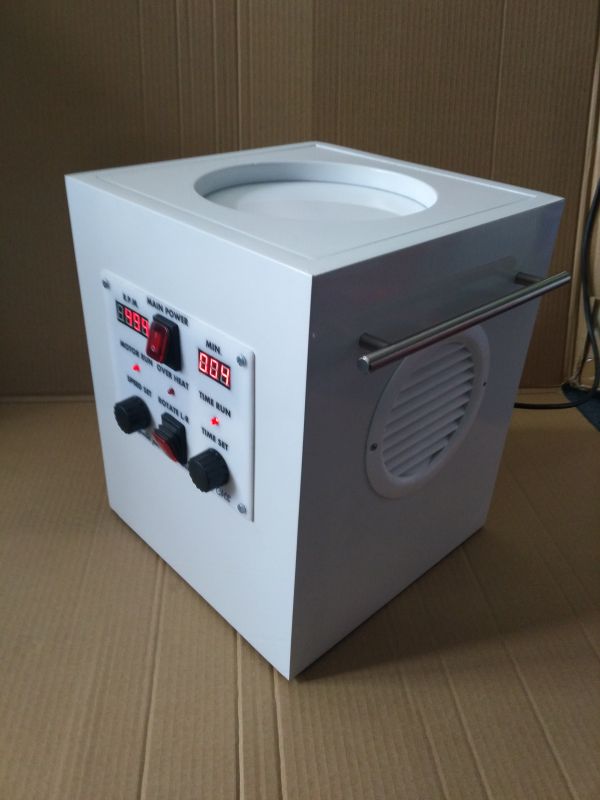
Das Endergebnis.
Wie ich bereits erwähnt habe, werde ich den Bauablauf der gesamten Konstruktion nicht beschreiben, da dies so lange dauern würde, wie die Konstruktion selbst. Sie haben Bilder zu sehen und Text zu lesen.
Vielleicht werde ich die Sicherheitsvorrichtungen erwähnen.
Wenn das Motorgehäuse 50 °C überschreitet (was während der Tests nicht aufgetreten ist), starten die Lüfter.
Wenn der Motor aus irgendeinem Grund (trotz laufender Lüfter) 85 °C erreicht, wird die Stromversorgung des Umrichters unterbrochen (die Lüfter bleiben natürlich mit Strom versorgt).
Und es gibt auch eine gewöhnliche 20-mm-Glassicherung.
An dieser Stelle möchte ich meinem Kollegen BESTLER danken für jede technische Unterstützung und Ermutigung in den Momenten, in denen ich bereits an diesem Projekt gezweifelt habe.
Cool? DIY-Rangliste